Battery Assembly Line
COSMEC GROUP Battery assembly line is a complete machine composed by various sub-stations. They are all connected by a common conveyor belt for automatic assembly of all types of batteries. The rapid change of battery type guarantees the wide range of batteries produced in the factory.
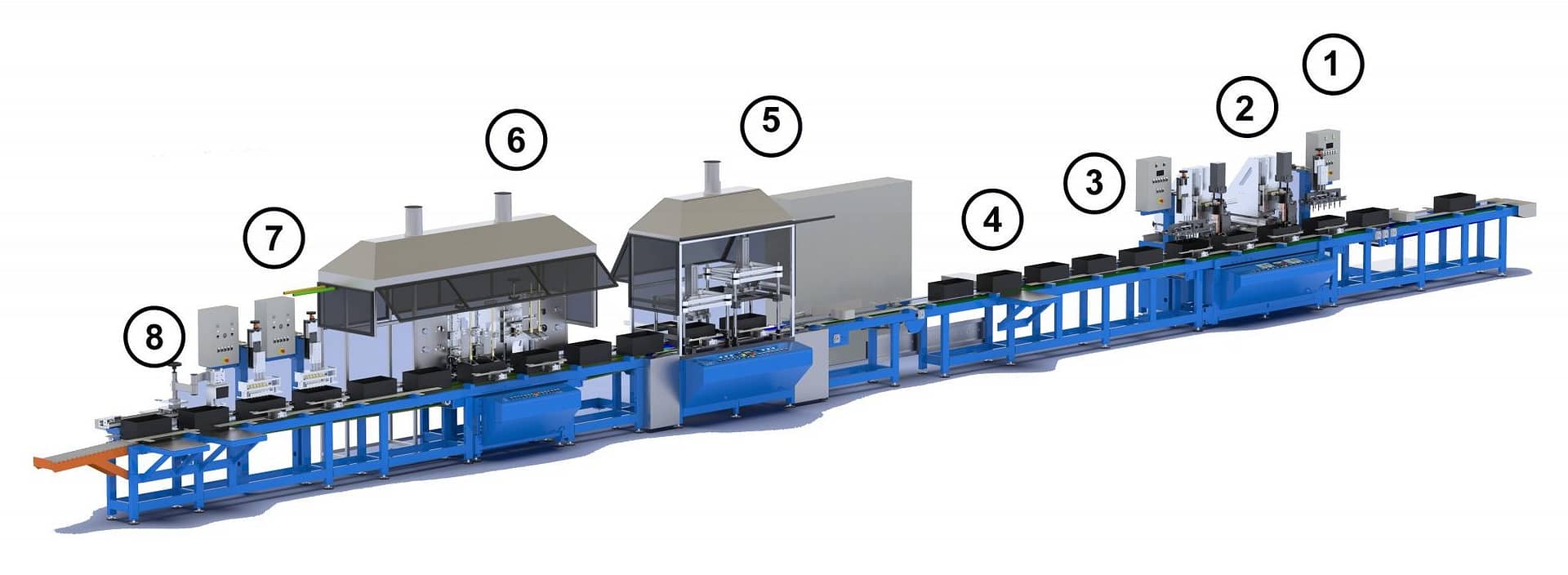
1
First short-circuit testing machine
2
Intercell welding machine
3
Second short-circuit testing machine
4
Automatic lid placing machine
5
Thermowelding machine
6
Post burning machine
7
Leakage testing machine
8
Serial number engraving machine
First short-circuit testing machine
The short-circuit tester is designed to detect short circuits in case of moist plates and separators. The machines allow the checking of the six groups inserted in the boxes; the test may be regulated by a potentiometer of voltage from the controlpanel.
In case a battery does not pass the test, it will be ejected on the first ejection station without any intercell welding process.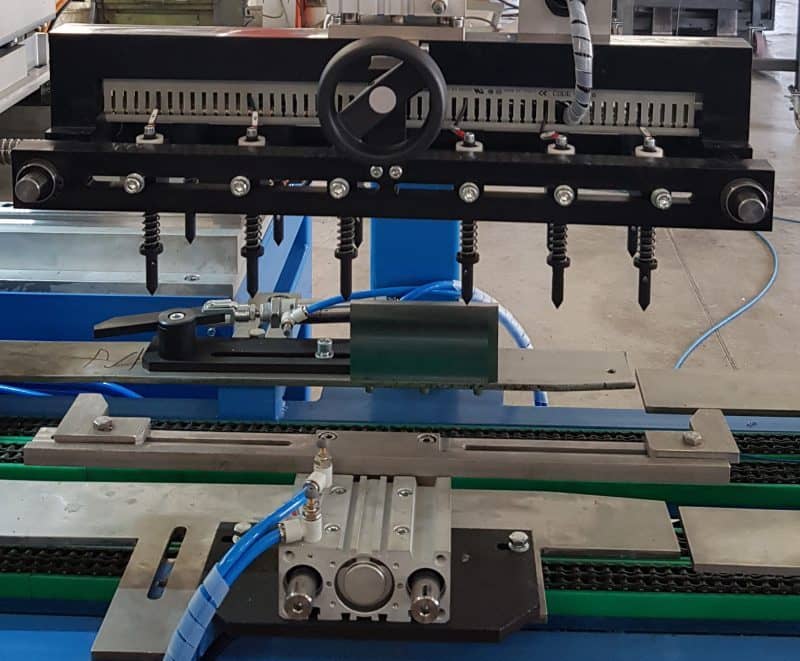
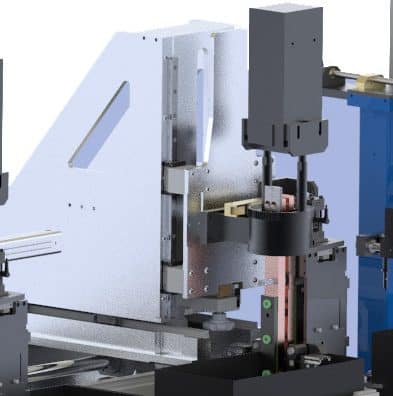
Intercell welding machine
The station performs welding of the straps to one another through previously made holes in the polypropylene. The machines is equipped with a couple of hydraulically controlled tongs.
The welding is performed with a high-density current, which is previously set on the control panel. 90 degrees automatic rotation of one of the heads allow the machine to weld also truck batteries without the necessity to stop the production for set-up.Second short-circuit testing machine
The machine ensures that there is no short-circuits between different cells of the battery.
Position adjustment along X and Y axes of the probes is guaranteed by a servomotor drive.Automatic lid placing machine
The station operates by taking stored lids and through a precise “pick and place” system automatically puts the lid on the corresponding coming by the conveyor from the previous stage of the assembly line.
Thermowelding machine
The machines is used to seal the lid to the box through thermowelding of both.
The hot plate is heated by resistances and is easily replaceable in case of format change. The optimal sealing is guaranteed by melting the contact surface of both the lid and the box before putting them back together. The process is composed by: arrival of the battery under the hot plate, picking up the cover, positioning the hot plate on the battery case and the cover on top of the hot plate, withdrawing of the hot plate and positioning and bonding the lid with the cover, drive off of the battery by the conveyor.Post burning machine
This stage of the assembly line is the final formation of the battery terminals. Under specific pre-fixed conditions (temperature and time), the battery posts and the flanges of the cover are welded together.
The temperature control is provided by water or oil circulating through the collared bushes where the post are burned.Leakage testing machine.
The machine tests the presence of damage on any internal or external wall of the battery as well as controlling the sealing of the cover. The leak detector is pressure and vacuum operating in the same time in order to check all cell of the battery in one cycle time. If any leakage causes a pressure and/or vacuum change the PLC gives one signal alarm. The sensitivity of the detectors can be adjusted according to the Customer’s quality standard. The set-up of the machine including the possible tool changeover, which covers a wide range of batteries, requires only few minutes. The head is equipped with six adjustable padded nozzles for injecting compressed air into the even battery cells and creating vacuum into the odd ones. The air and vacuum are fed into the battery until the pre-set values.
Serial number engraving machine
At the endof the line every battery is engraved with unique serial number to facilitate the following of the battery in the following stages and in aftermarket.